Backplane Connectors
What is a backplane connector and how is it different from a regular connector?
In system designs with modular architecture or multiple independent processing boards, where continuous, high-speed, and stable data transmission is required, the use of a backplane – a baseboard that connects these modules – is considered an essential solution. And the physical component acting as the interface between these boards is the backplane connector.
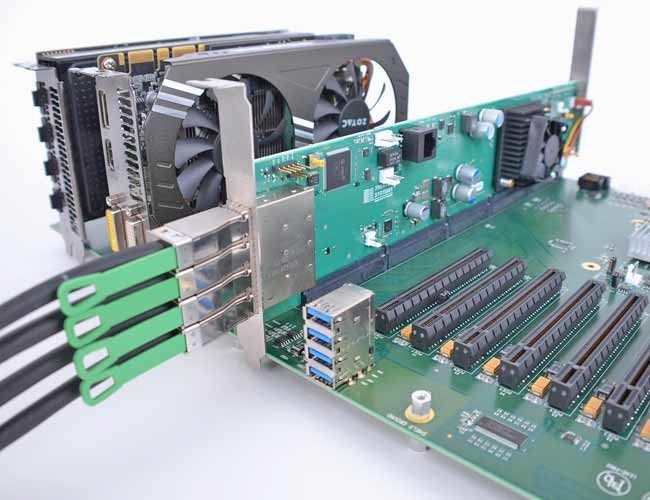
Unlike regular connectors that simply transmit signals between two independent components, backplane connectors are specifically designed for high-density, multi-channel transmission environments where signals may need to travel across multiple PCB layers with minimal loss. Their mechanical structures are typically right angle, stackthrough, or press-fit, offering precise mating and the ability to carry large signal loads without causing reflection or crosstalk.
Backplane connectors often need to meet stringent requirements for differential pair transmission, impedance matching, EMI control, and mechanical durability to withstand vibration and high-temperature environments – requirements that are not typically expected of standard connectors.
Why does choosing the right connector directly affect system performance?
System performance depends not only on the processor, software, or transmission architecture but also on the physical connection points.
In systems that use backplanes, where multiple boards exchange high-speed data through differential signal lines, connectors play a vital role in maintaining signal integrity. Choosing the wrong type of connector – for example, one with incompatible impedance, insufficient bandwidth, or poor conductive material – can lead to signal loss, reflection, or crosstalk, resulting in communication errors, data loss, or overall system slowdown.
What applications require high-speed backplane connectors (10Gbps, 25Gbps, 56Gbps…)?
In high-speed transmission systems such as modular servers, core network switches, high-performance storage systems, or telecom platforms using differential signaling, backplane connectors are essential for maintaining stable data transmission. These systems typically require transmission speeds ranging from 10Gbps to 56Gbps or higher, meaning the connector must ensure precise impedance, ultra-low signal loss, and excellent crosstalk suppression.
In addition to networking and datacenter infrastructure, high-speed backplane connectors are also used in industrial control systems with high-speed internal communication, advanced measurement equipment, or digital signal processing platforms. Some products in the EMIN portfolio include connector series from Amphenol, designed for transmission speeds up to 56Gbps and compatible with PCIe Gen4, high-speed Ethernet, or InfiniBand interfaces.
When should press-fit connectors be used instead of soldered ones?
Press-fit connectors are designed to be mounted directly onto the PCB through a compression mechanism without the need for soldering. Their specially structured contact pins allow the connector to fit tightly into plated through-holes on the PCB and be held securely by mechanical force. This method is particularly suitable for systems requiring high reliability, reduced thermal stress, and minimal impact on surrounding components during assembly.
In practice, press-fit is often preferred in systems with high component density, multilayer boards, or industrial environments requiring fast maintenance. Compared to soldering, this method shortens installation time, reduces the risk of thermal failure, and allows for easy removal during maintenance or connector replacement. Additionally, in high-speed applications, press-fit can help maintain stable impedance and minimize signal reflection at contact points if properly designed.
Which connectors are suitable for environments with vibration, high temperature, and high humidity?
In systems operating under strong vibration, high temperatures, or high humidity – such as outdoor industrial equipment, military systems, aerospace, or telecom stations – connectors must ensure both mechanical durability and long-term signal stability. These harsh conditions can easily loosen contact points, oxidize contact surfaces, or crack solder joints if standard connectors are used.
To meet such demands, connectors with mechanical locking mechanisms, gold-plated conductive materials for corrosion resistance, and heat-resistant housings are preferred. Backplane connectors with press-fit structures or those with integrated locking features are optimal solutions, especially when combined with EMI shielding to reduce interference and protect connections in harsh conditions. When selecting connectors for such environments, it's important to check specifications for allowable vibration amplitude, operating temperature range, and moisture protection ratings according to IP or MIL standards.
-
-
-
-
-
-
-
-
-
-
-
-
-
-
-
-
-
-
-
-
-
-
-
-